Cryogenic Deflashing Machine Shot Blaster
We offer full range of equipment including cryogenic deflashing systems, cryogenic deburring machines with start-up assistance, training and process optimisation.
Cryogenic deflashing machine shot blaster is most preferred and sophisticated technology for flash removal of majorly all type of rubber, plastic parts having complex geometry with desirable flash thickness. Cryogenic deflashing machine can also be used in flash/burr removal of zinc-magnesium die cast parts.
With cryogenic deflashing, there is almost full possibility of flash/burr removal from parts having flashes at both outside, inside areas as well as critical areas where the manual deflashing is not successful or most often left not deflashed.
The cryogenic deflashing machine offered by us, has PLC/HMI based operation which helps operator for faster data inputs.
The structure is specially designed for quick installation, require less space and makes cleaning, maintenance more easy.
The machine frame and other critical component are made out of pure high grade stainless steel for strong built quality and longer life.
There are various features in our machine including data input saving option, hot spot connectivity for remote access to PLC/ software troubleshoot, safety alarms, different access code/password to operator and management.
Our machines are also CE compliance with fully enclosed and isolated cabinetry to reduce noise, frost built up and meeting global safety standards with optimal performance.
The consumable are : Liquid nitrogen (LN2), Cryogenic deflashing media and Electricity.

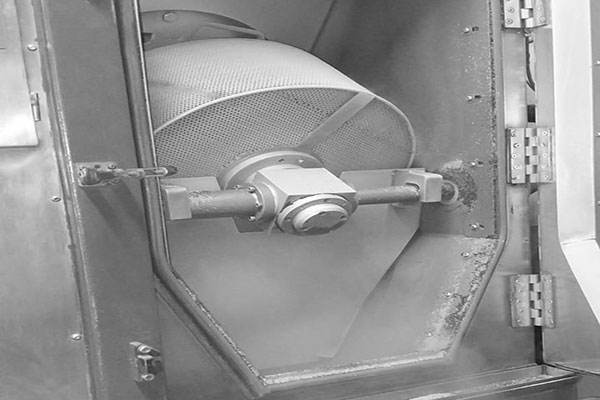
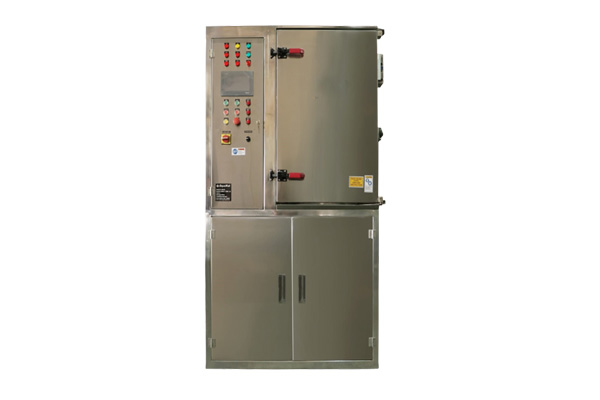
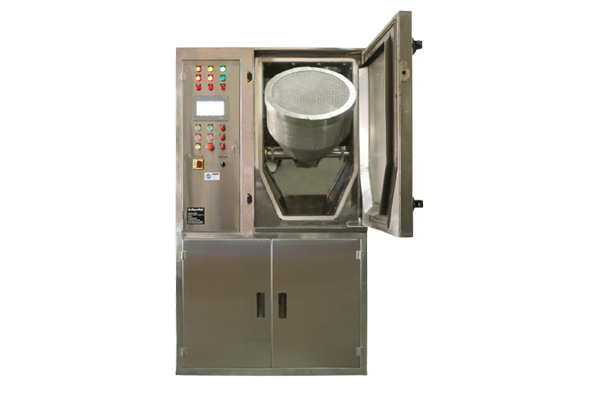


Cryogenic Deflashing Process
Cryogenic Deflashing process involves usage of liquid nitrogen (Ln2) and cryogenic plastic granulate/media in varying combinations to remove the flashes, burrs from a molded component in a highly precise, economical and efficient manner.
The cryogenic deflashing machine uses liquid nitrogen to help the ‘flash part’ reach a low enough temperature where its material becomes brittle. This stage is also called as ‘glass transition stage’ or GTS. The rubber or plastic parts are kept in a highly insulated chamber in which liquid nitrogen is sprayed where the parts are tumbled and blasted. This liquid nitrogen lowers the temperature inside the chamber up to minus 130 degree C. The difference in the thickness of flash and the part contributes to differential brittleness of flash V/s main part. The amount of liquid nitrogen and blasting material size are pre calculated depending upon the parts to be de-flashed. The blasting media then efficiently removes the flashes to enable the final finished parts to almost optimum accuracy.
During this process, the stainless-steel barrel rotates at defined input speed and once the material reaches a brittle stage, a unique high speed impeller directs deflashing media (made of polycarbonate, steel balls or any other type) on the parts with desired force. This results in a quick, effective and controlled removal of any residual flash of simple as well as complicated designed parts. Cryogenic Shot Blaster is useful for both outside flash removal as well as inside flash removal.
The physical properties of molded parts are not affected during the deflashing process and when the temperature return to its room temperature, the part gets back to its original shape – soft and the properties are not changed.
Cryogenic deflashing can also be used to alter or provide a polished or textured finish to a part’s surface.
Prerequisites:
Flash should be advisable to be as thin as possible (<0.25mm). Lesser the better.
Consistent mold quality. (preferred to have cryomold).


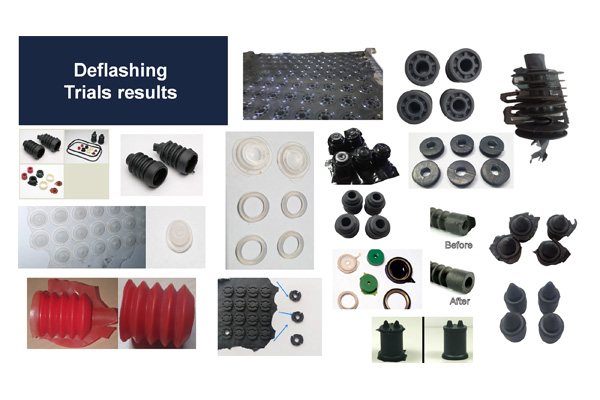


Application & Material suitability
Applications:
- Injection, compression, transfer molded parts.
- O-rings, gaskets and other rubber sealings.
- Auto precision parts like bushes, stoppers, bellows, washers, covers.
- Precision and complex structure irregular rubber parts (hardware, machinery gears, medical parts)
- Insulator and other microelectronic parts.
- Precision and complex rubber and plastic parts and many more.
- Clips, tags, dampers, electrical connectors, stands, switches
Material suitability:
- Rubber Material – NR, NBR, HNBR, CR, EPDM, FKM, Silicone etc.
- Plastic Material – PA+GF, PC+GF, PMMA, POM, PEEK, PBT, PPS, ABS, TPU, TPE, TPR etc.
- Die-cast Alloy – Zinc, Magnesium.